
EXHAUST HEAT SHIELD INSULATION
Exhaust Heat Shield Insulation
GoodFabs fabricates and installs the world’s best exhaust insulation for race teams, engine builders and supercar constructors.
Modern exhaust systems - particularly those used by turbo-charged engines - reach very high temperatures, so there is often a requirement to add a layer of thin metal foil enclosing a layer of microthermal material.
The purpose of the insulation is two-fold; keeping the heat inside the exhaust system to help the gases exit faster and to protect components and bodywork in close proximity to the manifold, turbo, secondaries and tailpipe.

Example of a non-insulated tail-pipe burning race car bodywork (seen within red circle)
Thermal insulation, or heat shielding as it is also known, is often a more expensive and intricate process than assembling the exhaust components themselves. The skills and technology required to cut, press and weld the thin (<0.15mm) metal foil are not commonplace and are only known to a few select companies around the world.
Sourcing the materials used in heat shielding is not straight forward as they are mainly used in the aerospace rather than the automotive or motorsport industry.
Heat shielding should not be confused with regular exhaust wrap or lagging, which attaches a layer of metal or tape directly to the pipework.
Heat shielding carried out by GoodFabs always involves a separate layer of microthermal or microporous material between 3 and 12mm thick, which is encapsulated by a fully welded covering of dimpled 0.1mm thick stainless steel or inconel foil.
This shield is then welded directly onto the exhaust system (integral) or pressed into a special shape (clam shell) that allows it to clip over the system and fit snugly around it.
When should I use heat-shielding?
Using an insulated heat shield around the exhaust system or the turbo can often help to increase the power output of engines with operating temperatures exceeding 800 degrees centigrade (around 1,500 degrees Fahrenheit) while limiting the thermal exposure of structural components and reducing thermal fatigue (in IndyCar, NASCAR, Rally, etc) just as a ceramic thermal barrier coating does, but with far better effect.
By cladding the exhaust pipes with thermal insulation, the outer surface temperatures drop significantly and contain the heat energy within the exhaust system.
What is integral insulation?
Data Sheets
Microporous Insulation Material
Adhesive Tape


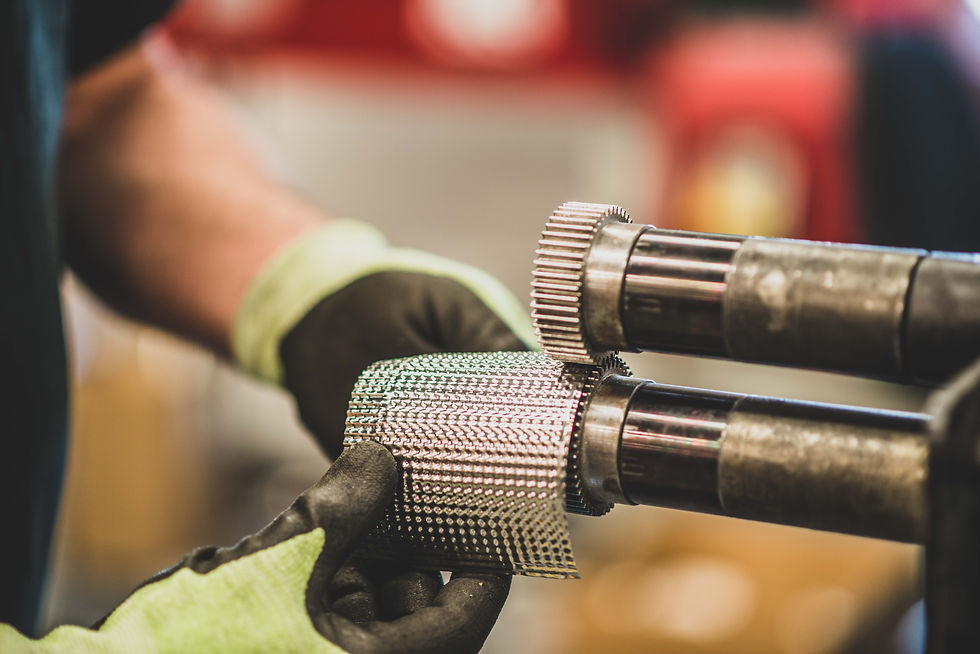
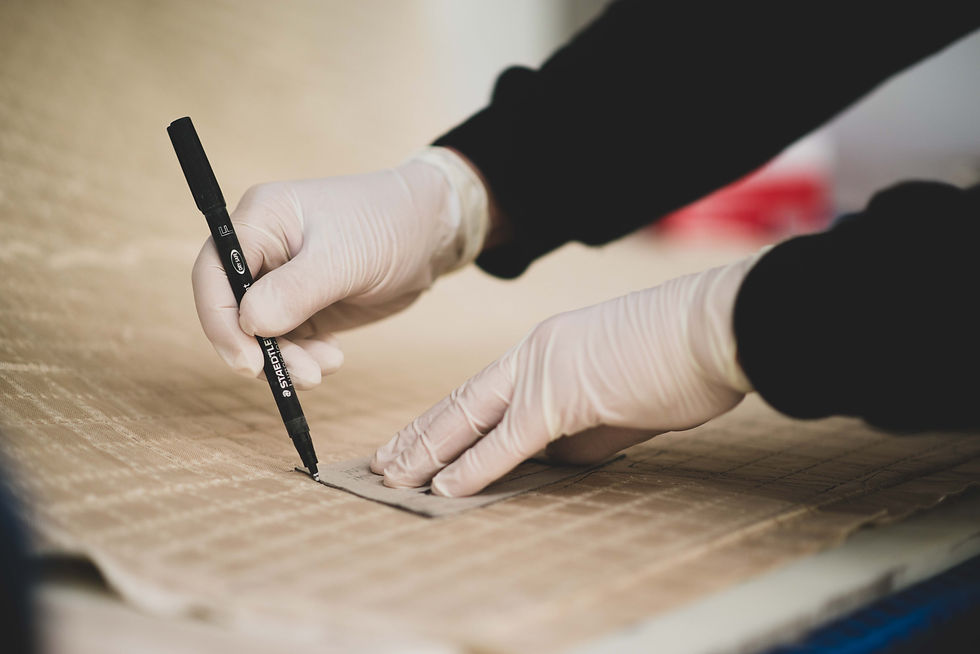
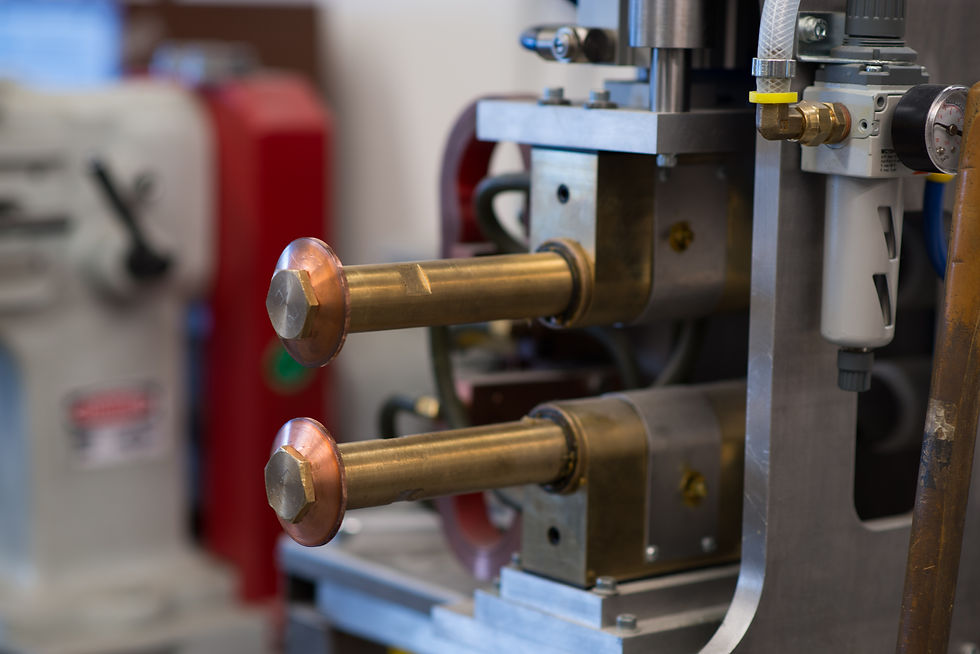
Specialised equipment is used for the heat shielding process

Microtherm material is cut to patterns and glued prior to enclosure

An assortment of dimpled foil pressings for use on integral or integrated heat shields
With the turbo having been re-introduced to Formula 1, unique exhaust heat management skills are needed to create heat shields which follow the exhaust contours perfectly, even with very complex geometry.
Each part is individually wrapped with insulation matting - microporous or silicate fibre are the most popular forms - followed by spot welding a dimpled stainless steel, inconel or titanium outer shell.
Custom-made press tools are manufactured in-house from CAD drawings to ensure that the shells are moulded to fit perfectly over the exhaust system.

3D printed jigs are often used to ensure that the integral heat shielding fits within the packaging constraints
What is clam-shell or clip-on insulation?

Clam shell heat shields with clips designed to fit around repackable mufflers
For exhaust systems that have more room in the engine bay or undercar area and are likely to be re-used or regularly removed, the clam shell option is sometimes preferred.
This form of heat shielding fits around the exhaust system and follows its contours without being welded to the pipes themselves.
Clam shells with clips or springs make it easier to remove the outer cladding which allows mechanics to perform non-destructive testing and early crack detection on the used exhaust pipes.
Clip on insulation features a dual layer of foil enclosing matting between layers so adds an additional layer of heat-shielding compared to integral insulation.
Should I use integral or clam shell heat-shielding?

Integrated heat shielding with dimpled 0.1mm stainless steel foil spot-welded to an inconel manifold and enclosing a microthermal layer to retain heat within the system
Integral or integrated heat shields are spot welded onto the exhaust system while the pressed clam shell heat shield is held together by clips or springs.
Your choice of type of heat shielding will depend on how much space you have and whether you are likely to work on or test exhaust systems for damage after they have been run.