Inconel alloys
- Didier De Lille
- Jan 15, 2017
- 2 min read
Updated: Apr 15, 2020

Download the special metals materials specification sheet here!
Inconel (nickel-chromium alloy) is widely used for its high strength and outstanding corrosion resistance in a large temperature range (from cryogenic to very high temperatures).
When inconel is heated, it forms a thick and stable oxide layer to protect itself from corrosions.
Since inconel can be used in such extreme environments, it is a perfect material for exhaust components such as turbochargers and tuned exhausts used in Formula One and NASCAR or other high performance motorsport applications.
Physical Properties/ Mechanical Properties
Inconel 625 is the most used variation of nickel alloys in exhaust systems. It is a non-magnetic, corrosion- and oxidation-resistant, nickel-based alloy.
Its outstanding performance, strength and toughness from cryogenic temperatures to over 1.000deg C are derived primarily from the solid solution effects of the refractory metals, columbium and molybdenum, in a nickel-chromium matrix.
Inconel has excellent fatigue strength and stress-corrosion cracking resistance to chloride ions.
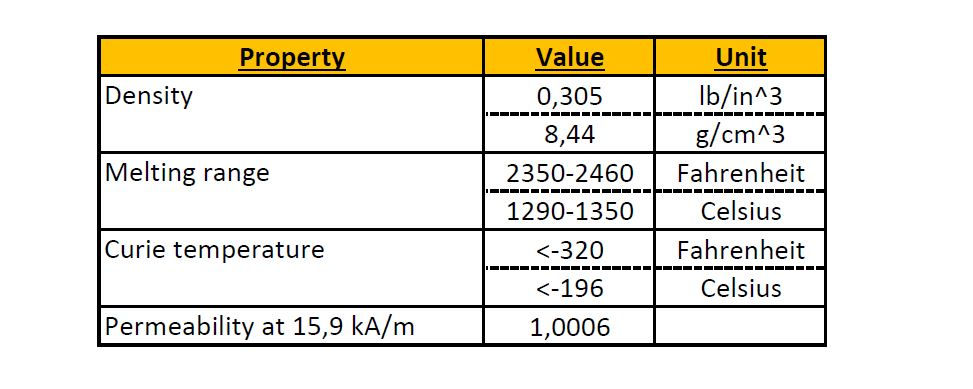
Composition
The strength of this alloy is drawn from the effect of adding molybdenum and columbium into the nickel-chromium matrix, meaning certain precipitation hardening treatments are not needed.
Due to the combination of these elements, the metal has an unseen corrosive resistance.
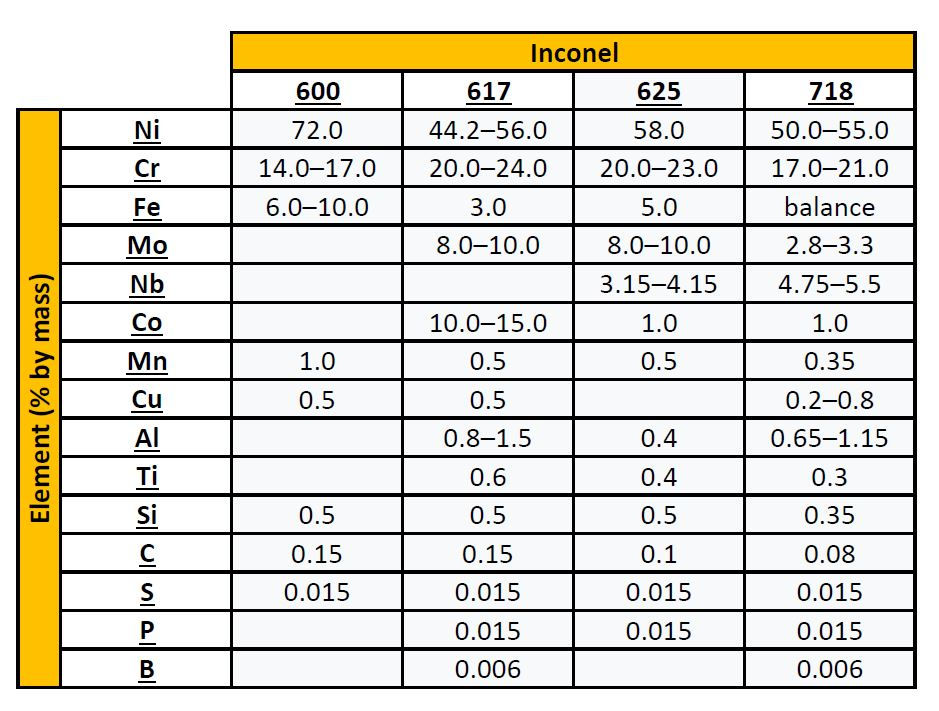
Machining and Welding
Since inconel is a metal which work hardens, it is difficult to shape and machine using conventional methods.
For example, with every machining pass, the material would either damage the tool or deform itself.
At GoodFabs, we have developed a technique in our machining department where we can machine the material with a hard tool and aggressive but slow cut.
An alternative to machining is to cut the material with a waterjet cutter or wire eroding.
The welding of inconel is difficult, which is why we have the best welders and fabricators working for us.
One of the biggest problems is that inconel is prone to cracking and segregation on the microstructural level where the heat is added to join the two pieces.
Comentarios