
PRESS FORMING
Press Forming
We are often asked to create irregular shapes that cannot be made using the fabrication methods that we use to bend or form tube. Transitions that go from oval to round are one example and complex collectors that gather multiple pipes into one are another.
Over many years of making complex exhaust parts, we have developed techniques to press out shapes using patterns and press tooling, designed and made in-house at GoodFabs. These shapes are then welded together to form whole parts.
Press forming is a cold forming operation used to create irregular shapes or bends which cannot be created using conventional bending methods.
Using a hydraulic press, where every stage is fully controlled by the operator, allows us to create parts with a more consistent wall thickness on very thin-walled materials (such as inconel, titanium, etc) than other cold forming processes.
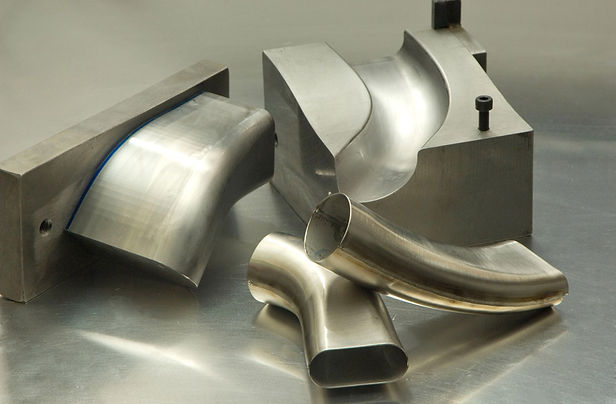
Oval to round pressed and welded inconel transitions for 2008 Honda V8 Formula 1 manifold
Compared to hydroforming, press forming complex exhaust parts is a more manual process but one that also benefits from longer productions runs.
This technique is both quick and accurate and particularly suitable for designs that change from week to week. Our ability to design and machine press tools in-house means that pressings can be created quickly within days rather than weeks if a hydroforming process is used.
The constant flow of press work that we carry out also means that the results are uniform and are closely inspected for repeated accuracy.
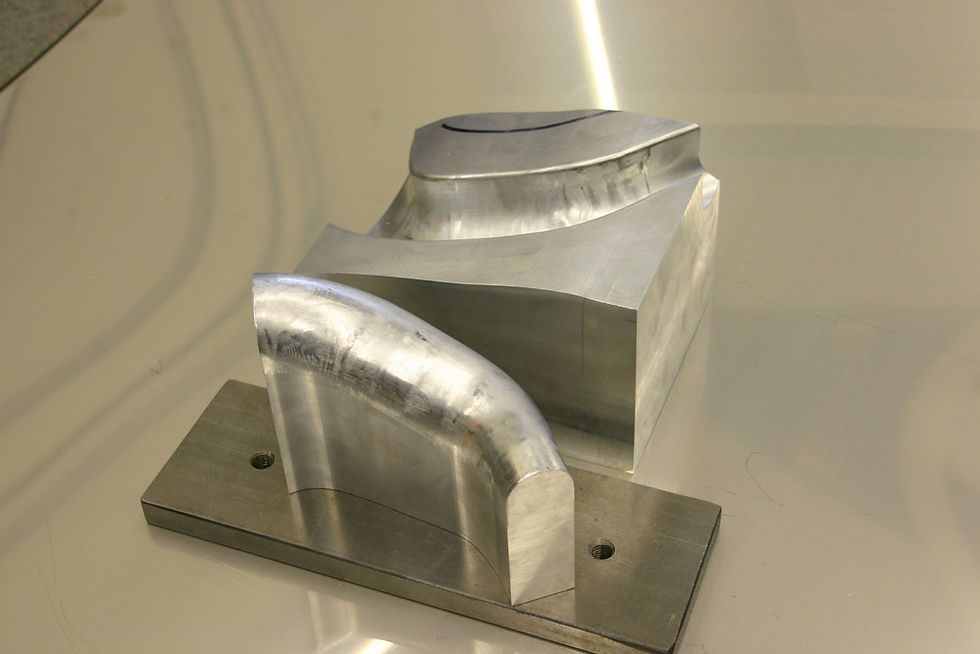
Press tool for an exhaust part for the Ducati 1098

Press tool for an exhaust part for the Ducati 1098
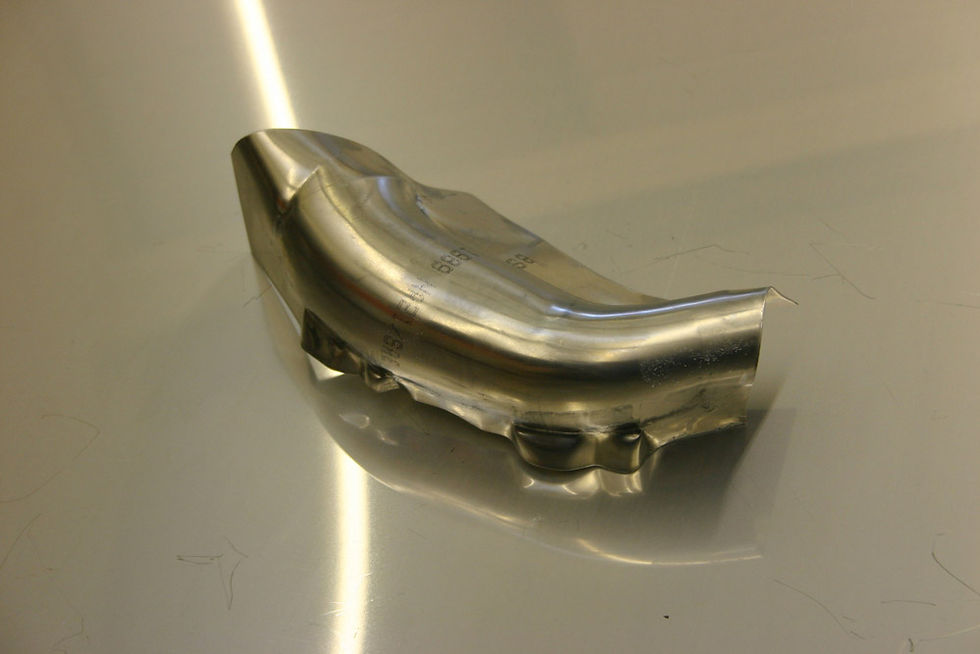
Pressed exhaust parts for the Ducati 1098
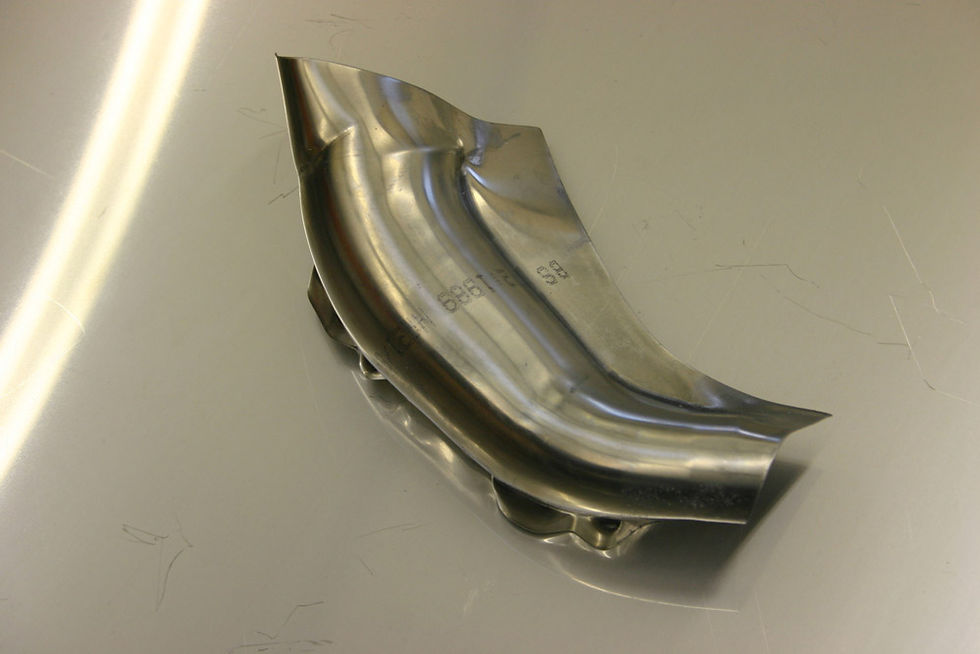
Pressed exhaust parts for the Ducati 1098

Welding two pressed halves to fabricate an exhaust part for the Ducati 1098

Welding two pressed halves to fabricate an exhaust part for the Ducati 1098

Fully welded pressed exhaust part for the Ducati 1098

Welding pressed exhaust part for the Ducati 1098
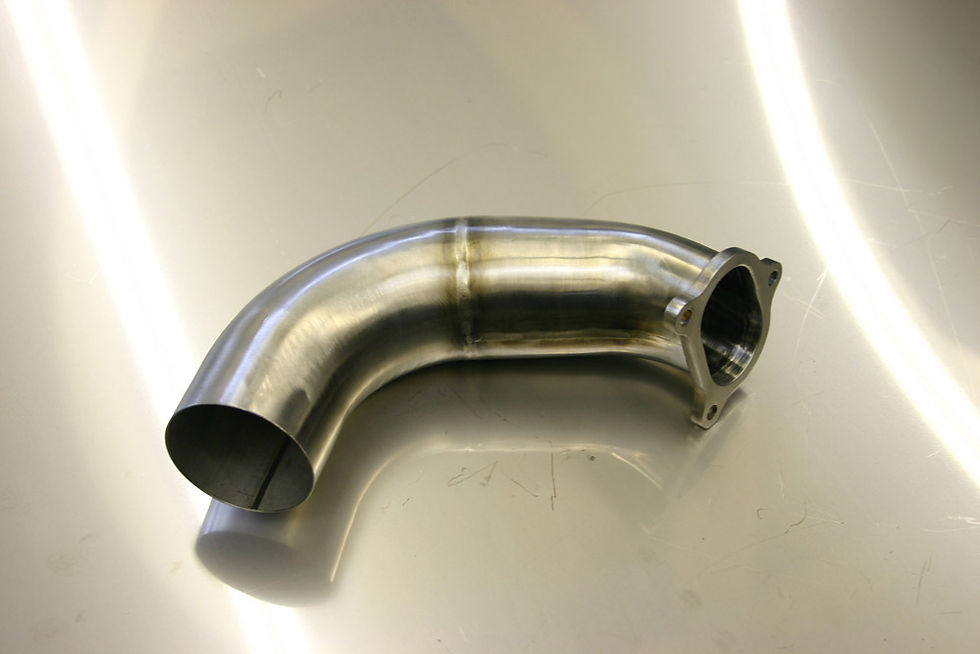
Finished, pressed and welded exhaust part for the Ducati 1098
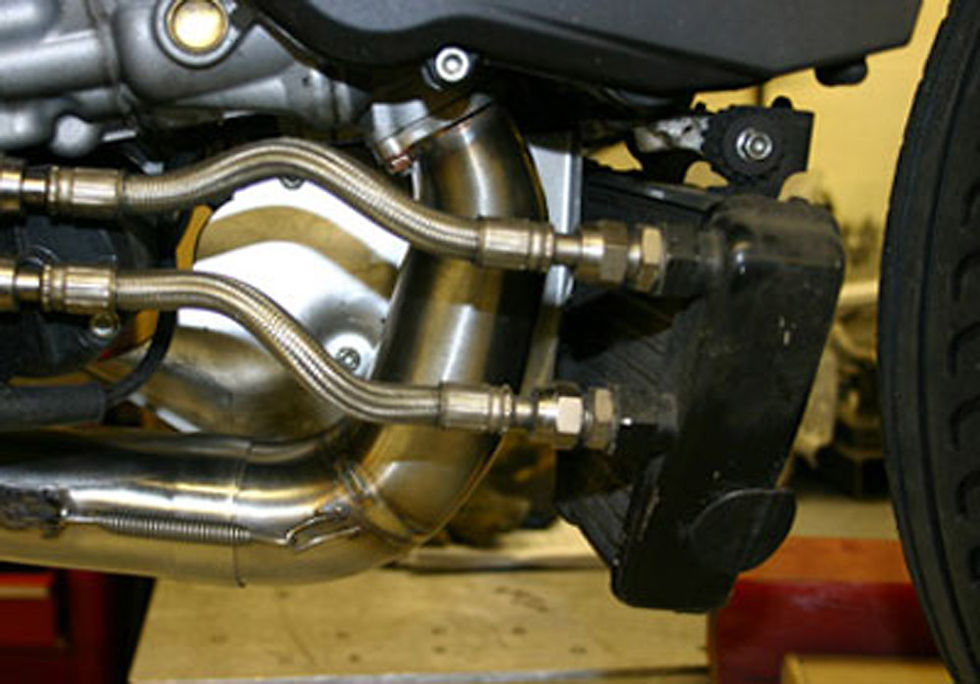
GoodFabs pressed, welded and fabricated part on Ducati 1098 inconel exhaust system