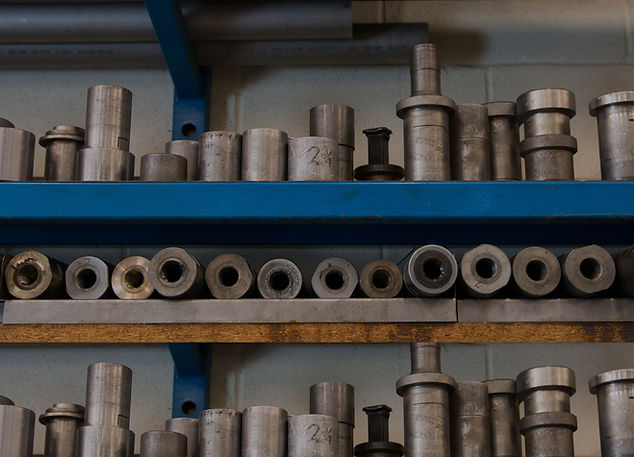
TUBE BENDING
Tube Bending
GoodFabs has a worldwide reputation for mandrel bending Inconel 625, 718, Stainless 321 and 304, grade 2 Titanium and Aluminium bends for race exhaust fabricators and race teams that fabricate their own exhaust systems.
We custom bend tube in diameters from 1" (25.4mm) to 3 1/2" (88.9mm) and specialise in Inconel bends and pressings.
Please note that all our bends are produced with a minimum clamp and are supplied untrimmed. If a specific clamp and tail length is required or you would like us to trim your bends to a specific length, please state this on your enquiry.
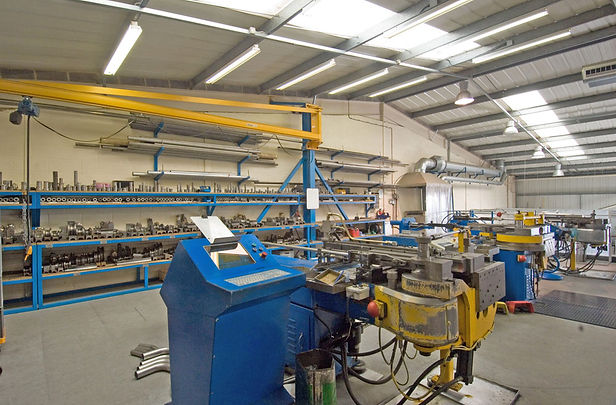
35 years of mandrel bending for top motorsport teams has required a significant investment in mandrel bend tooling, largely supplied by Tools For Bending in Denver, Colorado.
All our inconel tubes are made completely in-house from a flat sheet, giving us full control over all the aspects, enabling us to create high-quality tube bends.
As we have a large range of custom-made mandrel bend tooling to bend thousands of combinations, we have created a downloadable tooling chart allowing you to design an exhaust system or fabrication which can actually be made.
Mandrel Bends
All our bends are created using a linked ball insert while they are being bent. The tube is given extra support and we can reduce wrinkling and avoid breaking the tube during the entire bending process. This linked ball insert is called a mandrel.
Since we have been creating motorsport exhausts for over 30 years, we are able to supply engine builders and top motorsport teams, with the best quality mandrel bends, which ensure the best tubular consistency possible (see ‘Mandrel bending vs hydroforming’ article).

Multiple mandrels are used for various wall thicknesses of the same diameter tube at GoodFabs
Our expert tube benders use the correct mandrel in the bending process to maintain the nominal pipe diameter. This is achieved by allowing the outside of the bend to stretch and the inside to compress. We have multiple mandrels for each outer bend diameter to accommodate the wall thickness of tube required to achieve the lightest weight possible.
By keeping the nominal pipe diameter throughout the bend and the entire exhaust system, by using high-quality mandrel bends, the hot exhaust gases can maintain their velocity and efficiency.
Contact us for further information on our tube bending capability or download our tooling chart.
Mandrel bending vs hydro forming

A four ball mandrel for bending nickel alloys

GoodFabs has the largest range of mandrel bend tooling for alloys outside aerospace

Clark and Lewis mandrel bender with tooling
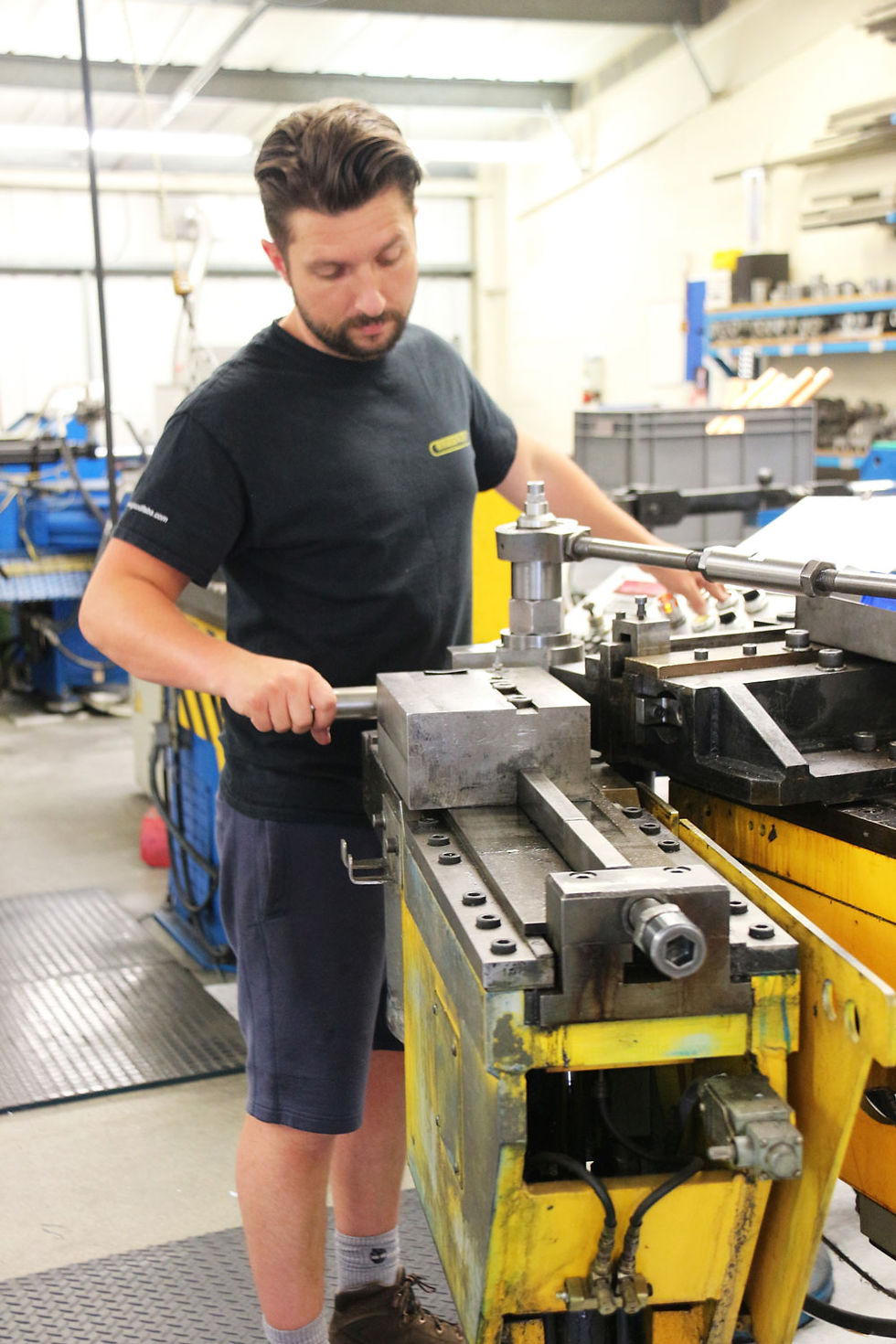
Mandrel bending hand formed inconel tube

Mandrel bending inconel tube

Mandrel bending inconel tube

Mandrel tube bending machines and bend tooling

Steel and ampco bronze bend tooling
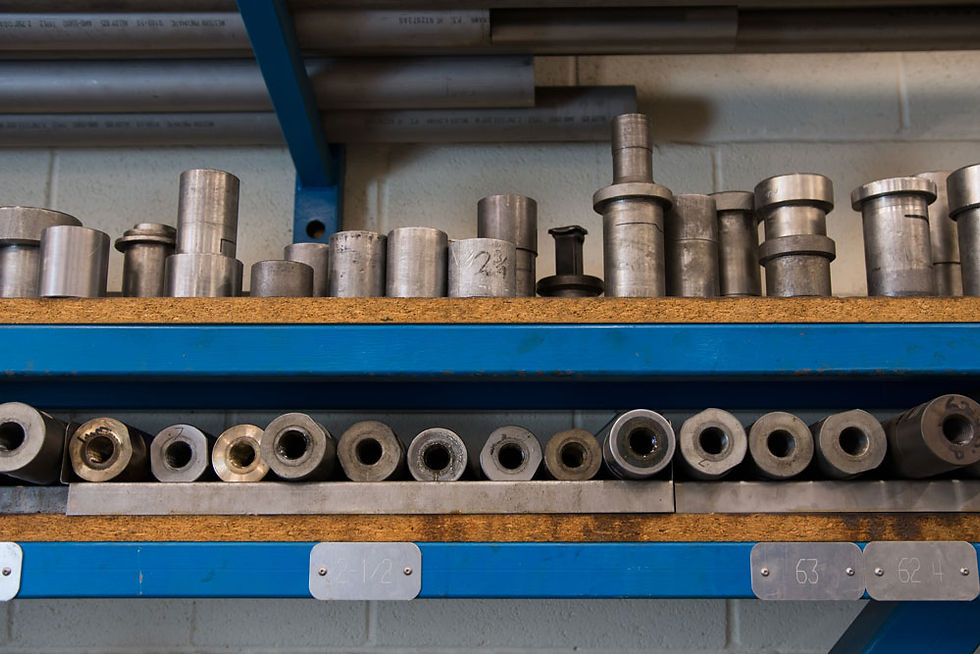
Steel and bronze mandrels for bending inconel and titanium tube