
WELDING
Welding
The TIG welding process mainly refers to Gas Tungsten Arc Welding or 'GTAW'.
TIG welding requires only three components: heat, shielding and filler material.
The heat is created by an electric current passing through the tungsten and arcing to the metal to be welded. This forms a ‘puddle’ of molten metal where the filler material can be dipped in by hand.
The shield is created by a protective gas flow around the heat affected zone, effectively reducing the risks of contaminating the metal with atmospherical elements.

TIG welding thin wall Grade 2 titanium at GoodFabs

Welding aluminium with a Furick Cup

Welding aluminium with a Furick Cup

TIG welding exhaust parts with extraction
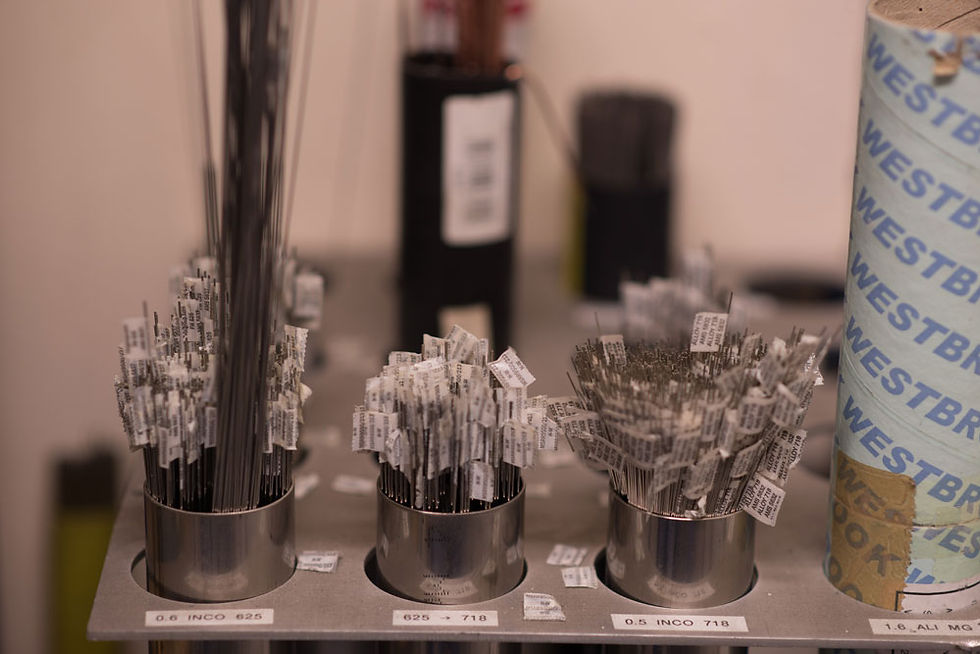
Inconel welding wire

Polished F1 V8 inconel manifold without collector

Polished full Honda F1 V8 inconel exhaust system

Polished full Honda F1 V8 inconel exhaust system mounted on flange plate

TIG welding an exhaust part
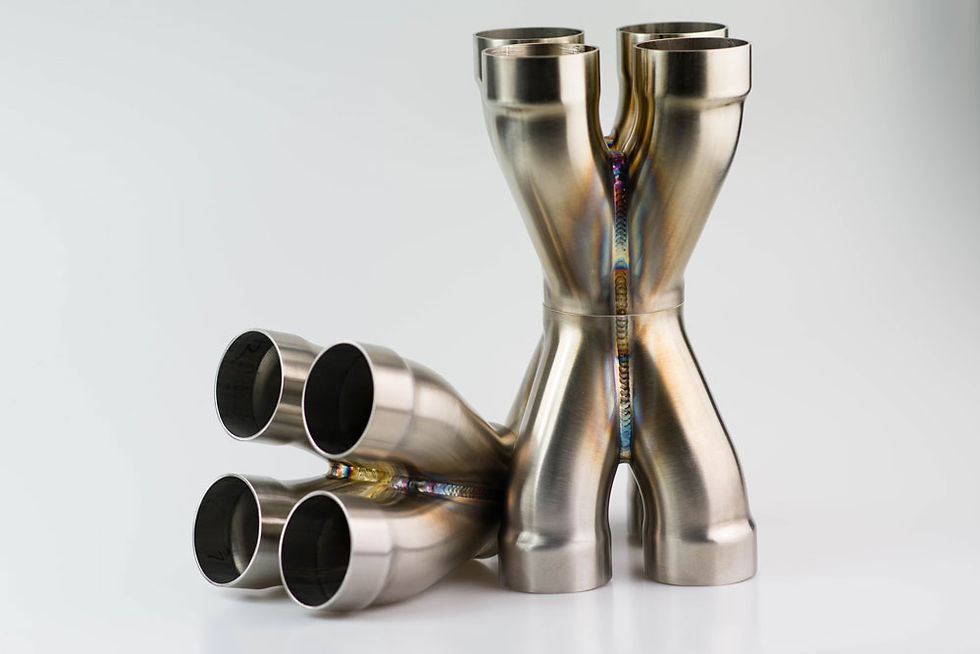
TIG welded stainless steel 4-into-1 collectors

TIG welded stainless steel 4-into-1 collectors
The ability to soft start and stop the heat makes the TIG welding process an ideal process to weld thin-walled material. With metals being as thin as 0.3mm, the slightest gap or mistake can cause a hole or large inconsistencies in the welds.
At GoodFabs, we closely monitor the weld quality in our inspection department which can perform a detailed NDT inspection.
Another large advantage of TIG welding is the uncleaned finish; a good TIG weld is so clean that it does not require any cleaning up or grinding to smooth it out, making it ideal to weld thin walled exhaust systems where the exhaust gasses flow at high speeds and any inconsistency might reduce the power output of the engine.
Welding thin walled exotic materials such as inconel, titanium or even stainless steel and aluminium require a perfect fit and very good welders.